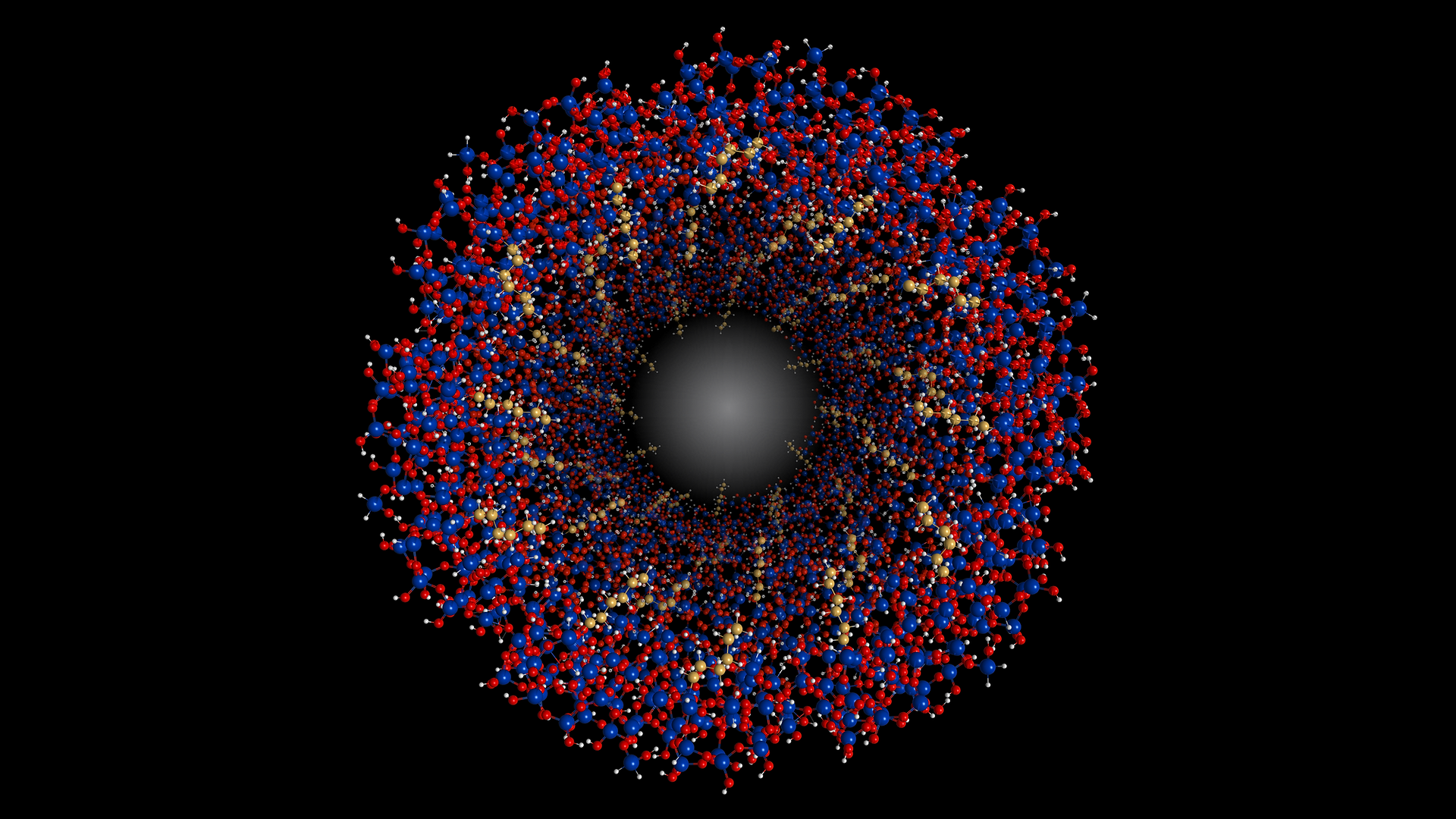




Welcome to
The Slowing Group
at Iowa State University
and the Ames Laboratory
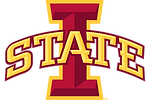




Left: Carboxylic acid-terminated modified Ames Lab logos (AL-COOH) 3D printed in different sizes. Right: Amine-terminated 3D prints (AL-NH2) after reaction with fluorescein isothiocyanate.under visible and UV light.
The ability to 3D print catalytically active materials allows performing chemical tasks that otherwise are very hard to do. For example, 3D printing a catalytic adaptor for a cuvette allowed monitoring directly the kinetics of a heterogeneous catalytic conversion (3-component Mannich reaction) step by step using a standard solution UV/Vis spectrophotometer without scattering problems.

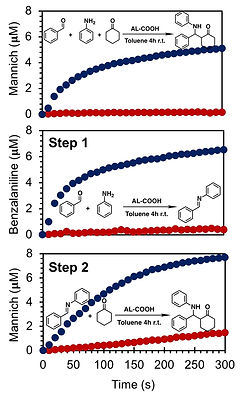

3D printing let us also produce directly millifluidic catalytic converters that already have the active sites homogeneously dispersed on the reactor walls. (62)

In collaboration with Helena Khazdozian and Ikenna Nlebedim of the CMI we are also using this approach to recycle magnetic swarf to 3D print magnets for diverse applications and to prevent waste of technologically relevant materials. (67)


Collaborators:
Aaron Sadow (group)
Ikenna Nlebedim (group)
Sebastián Manzano Hsin Cindy Wang
3D Printing of Chemically Active Architectures
We are developing methodologies to directly produce macroscopic structures having molecularly defined active sites via additive manufacturing. To this end we have developed an approach consisting of incorporating functional materials into 3D printing precursors. These precursors keep their properties after printing, allowing us to directly produce functional architectures. For example, in collaboration with the Sadow group we have produced catalytically active architectures displaying acidic, basic, amphoteric groups or even metal complexes.
